Choosing a Wood Floor - Step 5 - Hardwood Floor Finishing
STEP FIVE: The finish applied to the surface of your wood floor is intended not only to protect, but also to provide a level of shine or sheen that enhances the natural grain of the wood. When you consider the quality of the finish of your floor, think about the type of finish to be used and the preparation of the floor prior to finishing.
Wood Floor Sanding and Pre-Coating Preparation
The durability and quality of the finished floors are not dictated by the coatings alone. The sanding and finishing process is absolutely critical to the overall quality and longevity of the floor. This is the step that many contractors fail to perform correctly.
Since many homeowners cannot control or monitor this process due to their lack of technical knowledge, corners can be cut to finish a job faster in an attempt to maximize profits. The cost? The durability and quality of your floor finish.
Mr. Floor follows a strict NWFA (National Wood Flooring Association) sanding sequence to ensure that the wood pores have been closed correctly during the sanding process. You may have heard people wonder why their floors are “soft”, dent easily, or absorb liquids due to poor sealing characteristics. These issues are all related to an incorrect or inadequate sanding process.
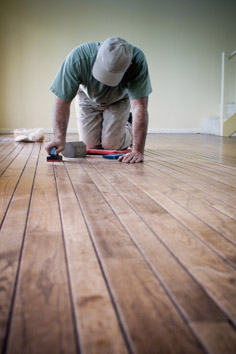
Wood Floor Finishes
There are several types of wood floor finishes popular in the Chicago market including oil-based, water-based, acid-cured and moisture-cured products. We have a very strong opinion on this subject.
Polyurethane Wood Floor Finishes
In reality, over 90% of Chicago wood floor installers will use either an oil-based or water-based polyurethane finish. The reasons are varied, but in general polyurethane finishes are more durable, dry faster and in the case of water-based polyurethane, are environmentally friendly.
Oil-Based Polyurethane Finishes
+Pluses
- Less expensive per-gallon
- Often more wear resistant than water-based
- Higher solids content may require fewer coats
-Minuses
- Takes longer to dry and cure
- Noxious odors from volatile organic compounds
- Changes color with UV exposure
Still the most commonly used urethane finish, oil-based “poly “ has been around longer than its water-based brethren and is often considered the “old school” finish. Oil-based polyurethane uses some form of mineral spirits as the major component. As a result, noxious fumes are emitted into your home as the mineral spirits burn off and the finish cures.
This off-gassing in an oil-based finish also takes longer to dry and cure than a water-based finish. This means that you will be out of your home for one to three days longer than with a water-based poly.
It used to be that oil-based polyurethane was more wear-resistant than waterborne, largely because of the higher solids content. The high solids content of oil-based poly also means that when applied properly, fewer coats are required to achieve the same coating thickness.
One reason that many wood flooring installers choose oil-based urethane Oil-based poly is that it is substantially cheaper than its water-based counterpart. Lower cost equals a higher profit margin for the installer working out of his truck.
Water-Based Polyurethane Finishes
+Pluses
- Fast-drying and curing
- Environmentally friendly
- Non-Yellowing
-Minuses
- Higher cost per-gallon
- More difficult to work with
- Requires a professional flooring contractor to apply property
Water-based polyurethane finishes were originally heralded for their quick dry times and low VOC emissions. Using an oil-based finish typically means that a customer cannot inhabit the home during the finish process because of the noxious fumes. Waterborne finishes solved this problem as volatile organic compounds (VOC’s) are minimized. And because water-based polyurethane dries to the touch and can be walked upon in 24 hours, customers can use the refinished space much faster.
There is a relentless and justified push to eliminate VOC’s from all commercial and consumer products and wood floor finishes are no different. Not only is the off-gas from oil-based polys hazardous to families and their pets, think about the workers applying such finishes day after day. Repeated exposure to the VOC’s in oil-based finishes, even with protective measures, is hazardous to a worker’s health.
Because water-based polyurethane finishes are at the cutting edge of finish technology, they are more expensive. This emphasis on research, however, also means that they are improving more rapidly than oil-based finishes. Today the best water-based products wear as well as oil-based finishes, if they are applied correctly.
Why We Only Use Water-based Poly for our Customers
If you’re looking to have an oil-based polyurethane applied to your wood floor, we’d love to chat with you to discuss your thoughts. Our number one priority is to satisfy our clients.
We’ll do our best to share our knowledge with and help you to compare an oil-based poly with a waterborne polyurethane that we use exclusively. If in the end you decide that an oil-based product is right for you, we’ll help you get what you want. Our hope, however, is that we can demonstrate why, despite the higher product cost, water-based polyurethane is the only product Mr. Floor uses.
At Mr. Floor, StepGuard is the only finish we use on our customers’ floors. StepGuard has been put through a series of tests by an independent lab that demonstrate its superiority. The scientific study shows just how durable, resistant and environmentally safe it is across the following dimensions.
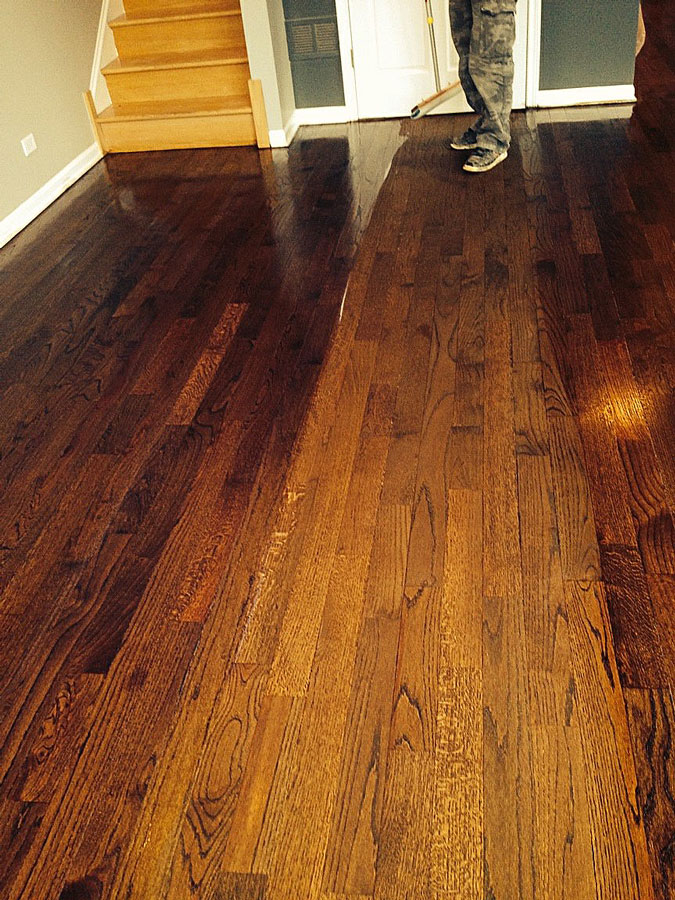
VOC Measurements and Ratings
The VOC rating is an industry-standard measure of the toxicity of a product. A lower measurement translates into lower toxicity. StepGuard contains 2.3lbs/gallon (276 grams/liter) of VOC’s as measured by the ASTM D3960-98 method. This rating is among the lowest on the market, but there are still enough organic compounds to maintain a superior level of durability.
The Taber Abrasion Test
The Taber Abrasion Test is the industry standard that quantifies the durability of a finish. The lower the number, the more wear-resistant the finish, since the number indicates how much finish has worn away from a given number of rotations of a test wheel. StepGuard rates at 21mg at 1000 cycles of a CS-17 wheel with a 1000lb load. This rotating “sanding wheel” simulates wear and tear over the years. In practice, StepGuards rating means you do not have to refinish your floor for a long time to come.
The Chemical Resistance Test
Spills happen, especially around a busy kitchen. Many ordinary household items have a potentially caustic effect on a floor finish. The Chemical Resistance Test measures how well the finish resists prolonged exposure to a variety of substances, from vinegar to nail polish remover. Using the ANSI A161.1-1990 24-hour test, we determined that StepGuard withstands most household items with virtually no effect.
Whether you’re looking for a gloss, satin or matte finish, StepGuard will provide a durable, safe, environmentally friendly finish that you can walk on and move furniture within 24 hours.
All Wood Floors Need Multiple Coats of Polyurethane
All unfinished or refinished floors need to have multiple coats of polyurethane for proper protection. With water-based products, three coats is what we consider standard, so be sure that your flooring contractor specifies the correct number of coats. While additional coats, properly applied can improve the appearance of the finish, too many coats can actually reduce the longevity, so please speak with your flooring professional
One last thing to remember. Though you can walk on a water-based polyurethane floor within 24 hours, we recommend that you do not put down rugs for at least 14 days. The final cure of the finish can actually take up to 30 days to reach maximum hardness.